新拓三维自研技术与设备,主要面向科研院所及工业制造等行业需求,以进口替代为主,目前在国内高校、研究所、企业已经近500家客户。
在材料测试、动态变形测试领域,三维应变变形及动态测试系统,在测量视场范围及其他核心性能指标达到国外竞品指标,实现国产替代。
在工业检测领域,先后推出了工业三维扫描系列产品、在线自动化检测方案、弯管测量系统,并开发了自主知识产权的工业检测软件。所有软硬件底层算法及核心模块均为自主研发,支持模块化定制,可灵活进行模块重组,打破了在工业检测项目中“卡脖子”现象。
未来,新拓三维将持续的进行模块化的开发、工业自动化检测平台,围绕工业检测、质量控制完成数字化通用化的测量检测终端部署方案。
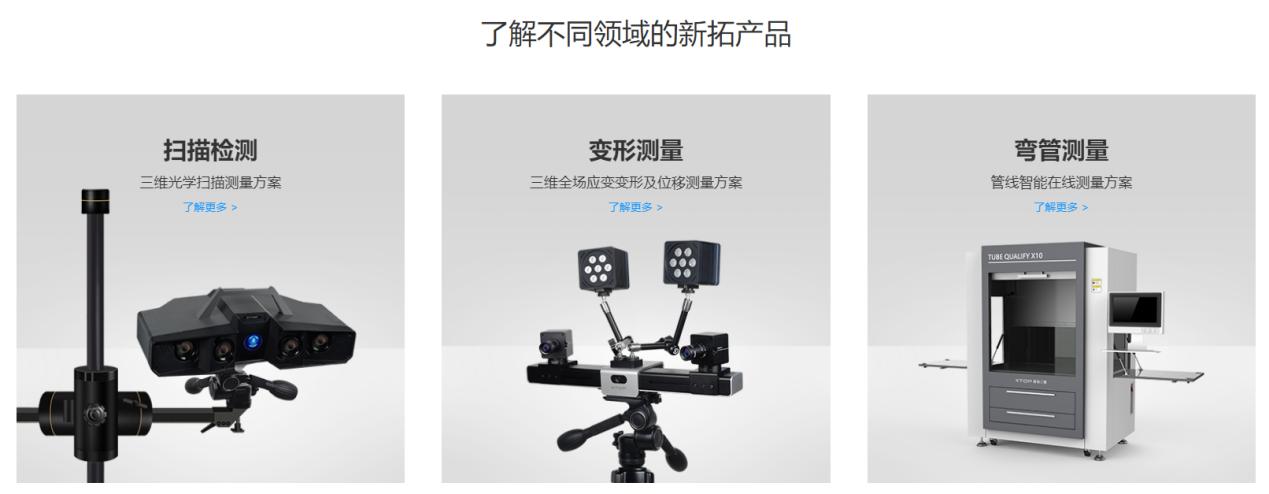
解决的痛点及需求
在材料测试领域:
随着新工艺、新材料的应用,高校、研究机构、机械加工制造业、3C电子产品、土木工程领域及医学医疗,都涌现出材料测试、产品性能测试、结构测试需求。传统的接触式测量技术存在测量时间长、需进行补偿、不能测量弹性或脆性材料等局限性,无法满足先进设计与现代工业发展的需要。国外产品存在不可定制、售后服务没有保障和贸易保护等问题。
新拓三维非接触式三维光学测量技术与产品,具有高效率、无破坏性、工作距离大等特点,适应复杂环境能力强,尤其对高温、高速、大变形、破坏等工况研究有常规测量无法比拟的优势,可以对物体进行静态或动态的测量,可以适应高低温、微观尺寸或高速运动复杂工况下的测试,可大大缩短产品的研制周期,是产品设计开发、验证模拟和材料性能测试的重要手段。
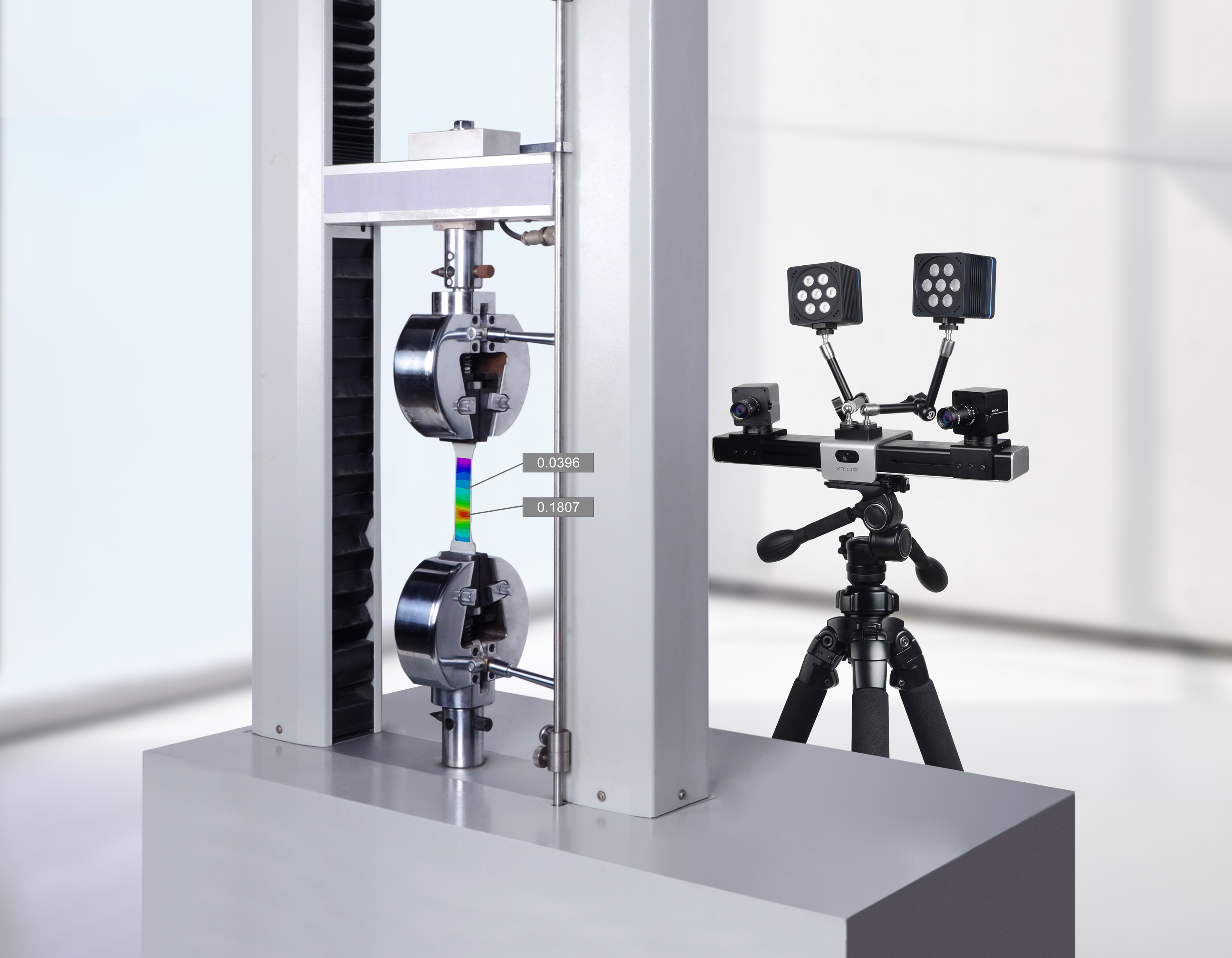
在工业检测领域:
三维光学测量技术应用在产品质量检测和工艺控制中,人工检测实现数字化的产线管理,使产能、质量水平和生产进度一目了然,实现产品质量监控追溯,大大提高良率、节约生产成本。
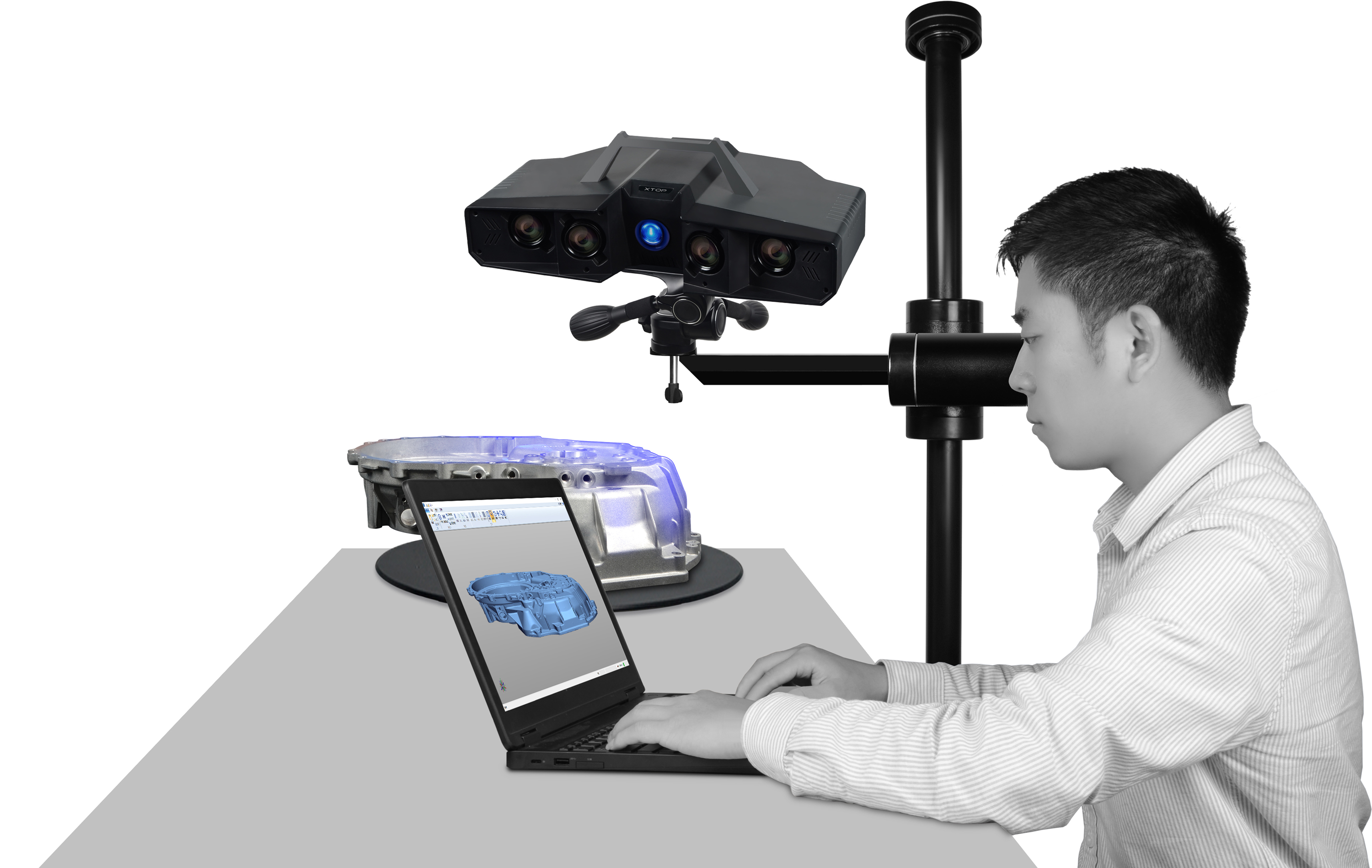
三维弯管检测系统颠覆性解决了传统管路检测使用检具的方式,实现航空发动机、汽车发动机油路和空调热管理管件的高效检测,同时减少了检具加工与储存成本。
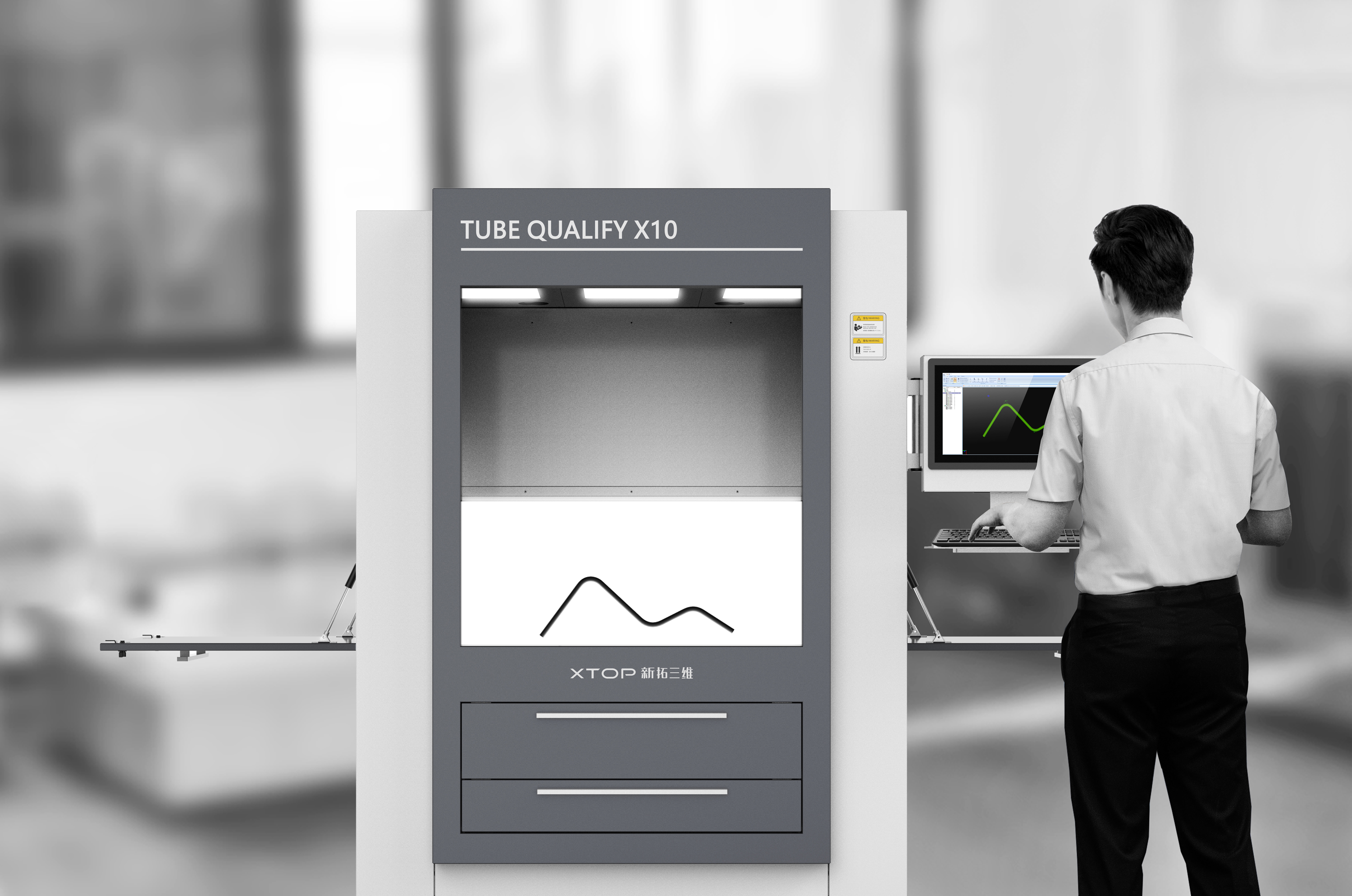
典型应用案例
作为国内三维光学测量检测领域研究较早、应用领域较广泛、技术与服务能力较为成熟的企业,公司系列产品和技术广泛应用于包括世界500强在内的众多国内外知名企业、研究机构、高校及科研单位的科研、生产和在线检测中,涉及消费电子,汽车制造,重型机械,生物医疗等行业,覆盖机械、材料、力学、土木工程等多个学科领域。
(1)积极开展与高校、军工企业、研究机构、半导体制造企业的合作,推广应用于材料、结构性能的变形测量与运动追踪的测试仪器;典型如清华大学、浙江大学、北京航空航天大学、南京航空航天大学、哈尔滨工业大学、西北工业大学、上海交大,航天一院、二院、四院、六院,半导体如英伟达、华星光电、华为等。
未来面向各应用场景打造细化方案和专用测试仪器,以及解决方案,如显微、芯片热翘曲,FLC,视频引伸计,材料本构分析,运动追踪,振动分析,红外系统,高速数据采集和实时处理等。
(2)与汽车整车、核心大部件配套企业和精密制造企业合作,开发应用于工业质量检测设备及自动化检测解决方案、核心部件,在工业互联网模式下,通过5G传输以自动化、嵌入式和云端计算为依托,打造完善的零部件在线检测方案。典型如天津汽车模具公司、瑞鹄模具、先锋模具、比亚迪、东风汽车、 中车唐山机车车辆有限公司等。
(3)围绕航天、航空发动机制造和航空器维修企业,积极开展弯管行业的调校装备、自动化产线建设改造解决方案与服务;典型如沈飞、5720工厂、成都国营锦江机器厂(5701工厂)、航天六院7103厂。
细化前端应用场景,丰富测量手段,提供包括设计在内的完整解决方案,实现软件平台化及分离部署,提供强大数据管理及分析能力,并积极主导行业测量及检测标准。
(4)在现有成熟产品与技术基础上,进一步加强对已有工业检测软件的开发,结合国家重点产业链规划,积极做好在产业链上下游技术的开发支撑和技术合作。
未来业务:慢慢转移向以三维测量系列技术的sdk开发与提供,最终以模块化的三维测量算法及软件、平台、标准化硬件模块为核心产品,为更多规模化应用的工业测量、自动化、智能制造企业提供底层标准模块。
应用成效和亮点
企业1:天津汽车模具股份有限公司
经营、设计、制造汽车车身内外覆盖件模具的专业公司,有近四十年的模具制造历史,曾为国内外诸多汽车制造厂家提供服务。
企业需求:
1.泡沫实型、铸件与模具检测,尺寸从几十公分到七八米,需要不同大小、形状都能检测
2.工厂无纸化生产管理,希望能实现数字化的检测检验;
3.检测结果直观,能以数据形式指导加工测量,测量结果精度要求,同时能缩减检测时间
解决方案:
在泡沫实型、铸件检测环节,引进了新拓三维XTDP三维光学摄影测量系统,实现现场数字化检测与结果传输,在检测中心专人进行软件分析,提高的质量与品控效率。
在模具检测和试制环节,采用了XTOM三维光学测量系统和自动化机械臂,进行固定检测工位的合格检验,覆盖了模具复杂曲面、冲压制件的全面检测检验。
企业2:三樱工业株式会社
创建于1939年,主要产品为汽车发动机管件,其汽车的制动系统和发动机系统的零部件销售拥有日本1/3市场份额。
企业痛点:
1.传统检测方式对复杂管线检测困难、效率低,无法在线检测
2.需要大量检具,存储与制造成本高
3.检测结果无法数据化、智能化
解决方案:
采用新拓三维Tube qualify管路三维光学测量系统,以非接触式柔性测量手段2秒内即可提供测量结果。系统结合机械臂形成自动化检测方案,检测和调机效率比传统手段提升数十倍以上,并可以对数据进行云端存储和生产过程的跟踪分析。非接触式测量,避免了检测过程中管件表面划伤造成的报废,降低了检具制作、存储场地的成本。同时,也应用于管路管件的逆向建模与注册,解决了人工手段需要数十次反复试验试制的方式,快速获取弯管原始数据,并能与弯管机器人通,解决了这一难点。
企业3:中国科学院金属研究所
成立于1953年,是新中国成立后中国科学院新创建的首批研究所之一,为国家重大工程提供关键材料。
企业痛点:传统测量方式在很用场景中使用受限
1.针对非常规柔性材料、大变形材质、恶劣环境等情况下的测试;
2.实验过程容易产生损坏,不能重复循环使用,长期成本高;
3.实验过程不可追溯,无法评估;
解决方案:
采用新拓三维XTDIC系列全场应变测量系统,应用与材料测试中的全场应变、特征轨迹跟踪测试与材料力学性能分析。系统有效的提升了测试效率、降低了传统测试手段使用的成本,实现了不同研究目的测试,无须重复试验。系统丰富的数据,提供全场应变、位移、变形、形貌,可直接测量全场振幅、振动信息;非接触式测量,也不会对样品造成损坏,对环境的适应性大大提升。