汽车轮毂轴承,作为汽车关键零部件之一,肩负着承重与精准引导轮毂转动的重要使命。它不仅能承受轴向载荷,还能应对径向载荷,确保汽车行驶的稳定与安全。
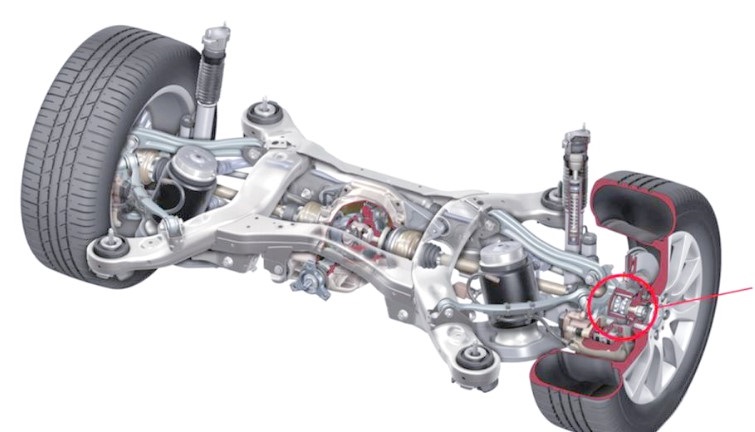
使用新拓三维XTOM工业级蓝光三维扫描仪,对汽车轮毂轴承模具进行3D全尺寸扫描,能够轻松高效地获取精准的三维数据,有效避免人为测量误差,实现3D全尺寸偏差分析,大幅提升模具的检测效率和质控标准。
轮毂轴承模具通常采用热锻工艺制造,高温高压下金属塑性成型的复杂性导致两大核心问题:
模具精度不足:传统检测、三坐标仪(CMM),检测速度慢,且仅能测量有限点位(覆盖率<30%),难以捕捉模具曲面的微小变形(如R角塌陷、型腔偏差);
热锻工艺缺陷:模具局部误差在热锻中被放大,导致锻件飞边、折叠、填充不足等缺陷,废品率高达5%-8%,并加速模具磨损(寿命缩短30%)。
蓝光三维扫描技术应用必要性
蓝光三维扫描技术以其非接触、全尺寸3D检测、高精度等特点,成为复杂轮廓曲面模具检测与工艺优化的理想解决方案:
全域数据覆盖:单次扫描10分钟内完成全模具表面检测(精度±0.01mm),数据密度达百万级点云;
精度与效率高:500-900万高分辨率工业相机,结合先进的三维扫描重建算法,能够实现高精度的轴承模具检测;可满足汽车轴承模具对于各种槽、孔和凸起等表面结构全尺寸检测。
工艺闭环优化:基于3D检测数据修正模具CAD模型,调整锻造温度、压力分布及材料流动路径。
汽车轮毂轴承模具三维扫描现场
采用新拓三维XTOM工业级蓝光三维扫描仪,在3D扫描数据采集过程中电脑实时显示扫描进程,完成后可以直接导出STL格式文件。
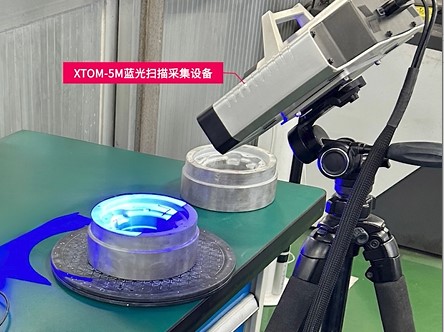
汽车轮毂轴承模具三维模型数据
XTOM工业级蓝光三维扫描仪快速采集模具的三维特征,测量尺寸形状以及表面的缺陷,高效地进行模具的形位公差检测,确保模具的生产质量。
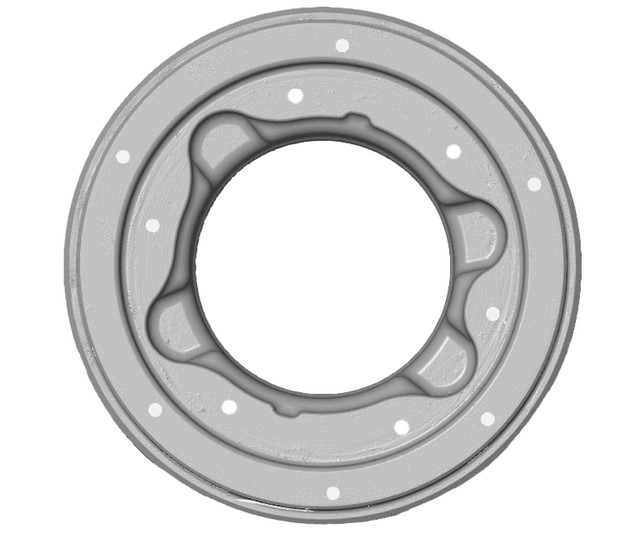
汽车轮毂轴承模具形位公差分析数据
将获取数据导入三维检测软件中,与原始CAD数模进行对比分析,生成简单易懂的偏差色谱图,为后续产品的修模、改模提供精准的数据指导。
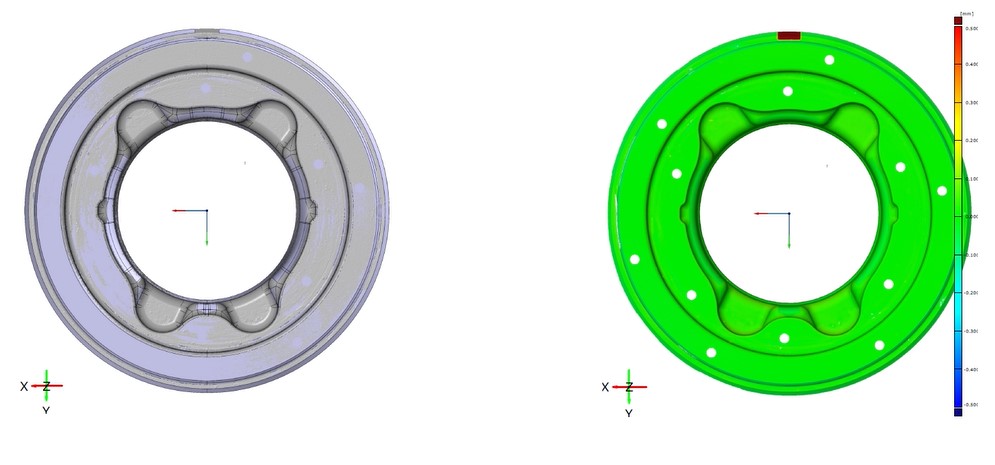
通过检测软件分析比对,任意位置偏差状况也可以数值化的显示,可分析模具平面度、圆柱度、孔位偏差等数据,可辅助工作人员进一步优化或调整加工工艺,确保成品符合设计要求及质量标准。
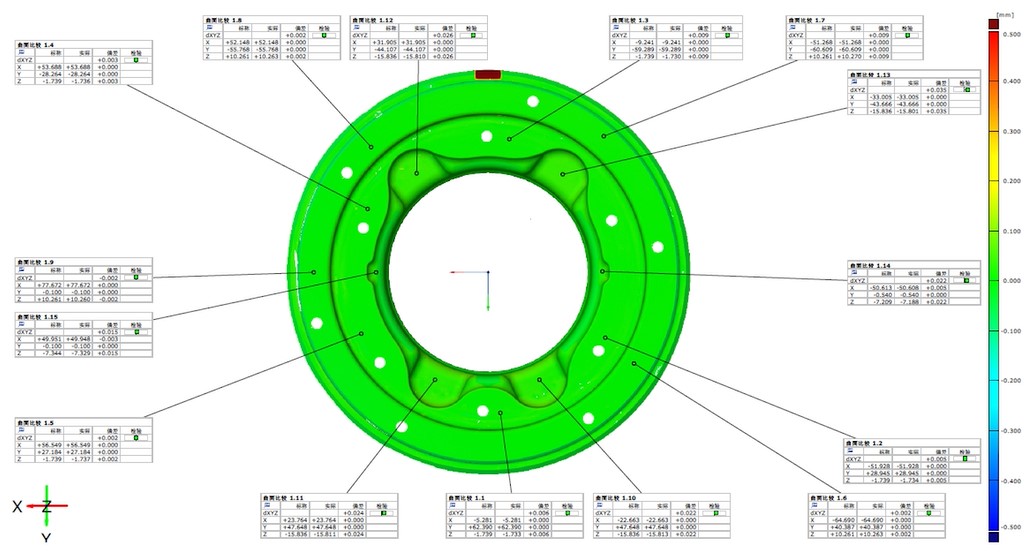
通过XOTM工业级蓝光三维扫描仪进行汽车轮毂轴承3D检测,有助于防止制造过程中的误差累积,加快新产品的开发与迭代;分析报告可进行数字化存档,作为制造过程各阶段状况的数字记录,以便后续质量追踪和管理,也为后续批次的生产及质量控制提供依据,确保产品的可追溯性。