一、项目背景
聚合物基复合材料具有较高的比强度、比刚度、耐腐蚀、可设计性强,在航空航天领域得到了广泛的应用,成为飞机、火箭、人造卫星、军工武器等结构上不可或缺的战略材料。随着聚合物基复合材料的大量应用,复合材料构件的失效也逐渐增多,且可能造成灾难性事故。
与传统的金属材料结构相比,复合材料在承受载荷或发生故障时的性能有着显著差异。因为复合材料通常是脆性的,不像金属通常是韧性的,后者在破坏前会变形。这些变量是复合材料所特有的,通过实验测试复合材料在荷载作用下的失效和破坏行为,可以为新材料及部件及的创新设计和性能提升提供数据依据。
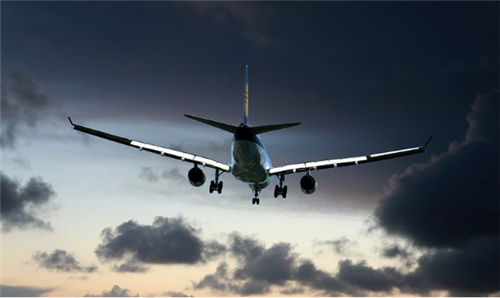
二、测量需求
由复合材料制成的部件,在应用过程中不可避免地会受到动态载荷的作用,而复合材料在动态载荷作用下的力学性能有着显著的不同,因此有必要对特殊材质的复合材料式样展开拉伸、剪切、压缩试验,并与传统的应变片手段进行对比。
三、原有检测方法
原有解决方案
电阻应变计是过去常用的应变测量方法,在结构表面安装应变片,受载后结构表面产生微小变形,应变计的敏感栅也随着变形,电阻相应发生变化,即尺寸变化转化为电阻变化,将电信号输入仪器进行分析,从而得到相应应变。
传统的复合材料应变检测方法,采用引伸计与应变片等接触式方法进行,应变片直接粘贴于式样表面,并通过接线的方式与采集箱连接,精度较高。
原有方案不足
应变计作为应变测量的工具,存在着贴片过程繁琐,使用繁琐,测量精度严重依赖其贴片质量。
对于纤维、膜等不适于粘贴应变片的材料和结构实验,接触式测量方式会影响试件本身的力学性能。
应变计量程有限,难以捕捉到关键位置的变形初始位置,无法测量大变形或断裂试件,影响测试数据的质量。
四、新拓的DIC测量方案
复合材料共有三个类别试件,各个复合材料特性均有所差异。需测试一种试件在拉伸时失效断裂,一种试件以一定角度剪切失效断裂,而在另一种试件中以压缩加载测试受力性能。采用新拓三维XTDIC三维全场应变测量分析系统对试件在加载下进行全场测量,并实时计算出位移场及应变场分布。
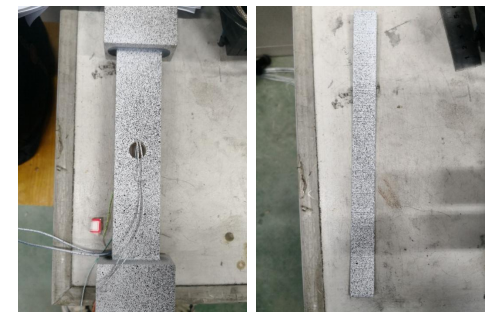
1、拉伸应变测量
利用万能材料试验机对复合材料进行拉伸实验,设置XTDIC系统的工业相机1秒1帧的采样速率,试验机与工业相机同步进行图像采集,直至复合材料试件破坏,停止加载并完成采集,并对采集数据进行计算分析,在试件拉力处获得全场应变试验数据。
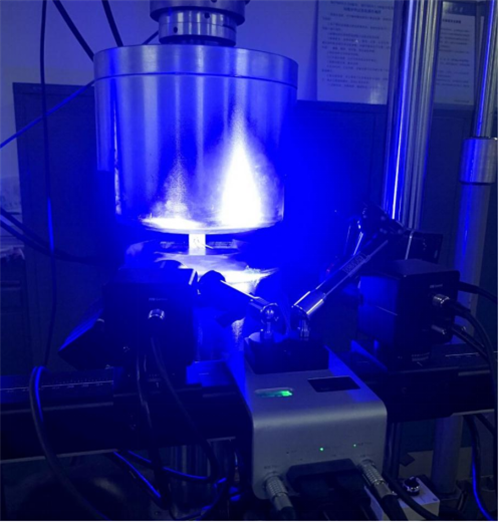
由于数字图像的离散性特点,DIC测量方法可快速计算以像素为精度单位的试件全场位移,输出试件测量的位移场。
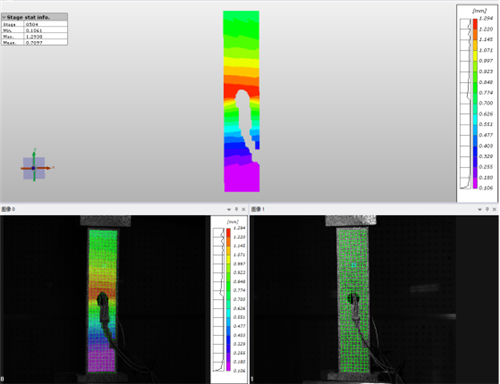
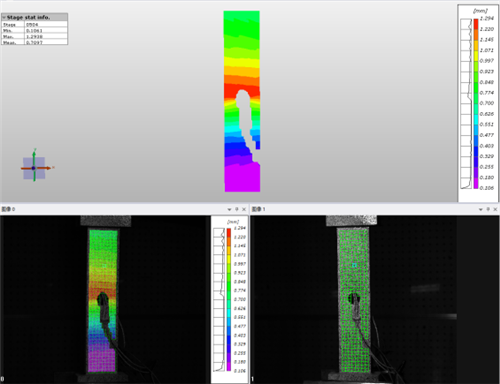
通过算法计算得到亚像素精度的全场位移,基于位移进行数值微分处理得到应变场,试件应变场如下图所示:
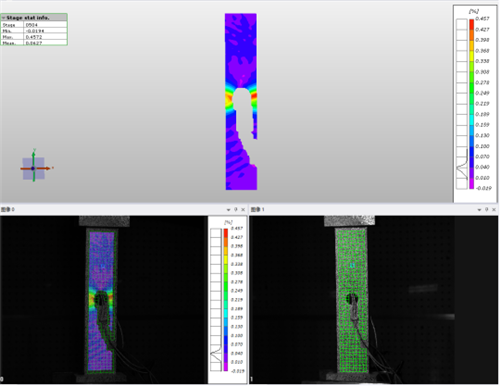
关键点应变曲线:
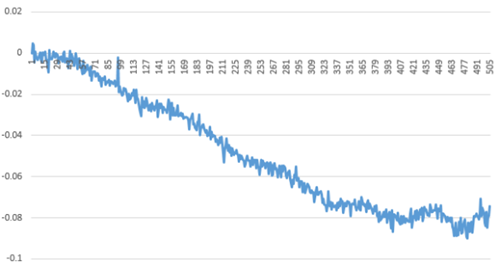
采用XTDIC系统对复合材料样件进行全场测量,可测试材料的抗拉强度、弹性模量、泊松比等特性参数,测试复合材料在受力加载时抵抗伸长变形的能力及断裂的特性。
2、劈裂应变测量
将碳纤维复合材料试件放在万能材料试验机上,借助夹具两侧杆将试件对中。试验机以连续、均匀的速度加载荷,直至试件劈裂为止,试验机与XTDIC系统搭配的工业相机同步进行图像采集,记录下破坏载荷,并对采集数据进行计算分析,获得劈裂过程全场应变试验数据。
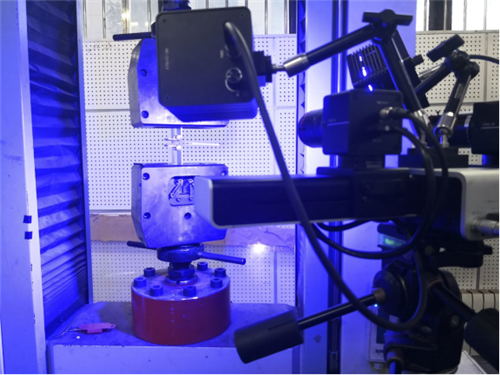
DIC测量方法可快速计算试件劈裂过程的全场位移,测试出试件裂缝的位置、形态、分布特征,裂缝发生及开展的时间过程,裂缝周围试件表观质量情况等,位移场如下所示:
基于位移进行数值微分处理得到应变场,复合材料在劈裂过程的相对位移情况一目了然,试件应变场如下图所示:
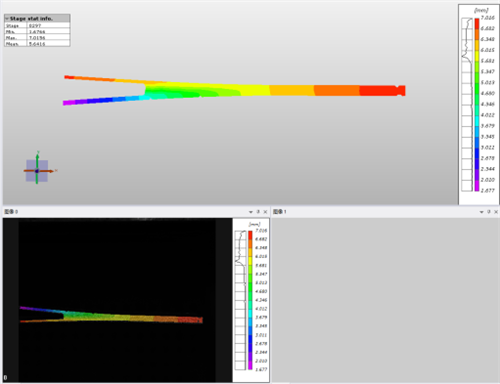
对复合材料的劈裂力学测试,XTDIC系统与试验机结合,实现材料应力-应变曲线、弹性模量、剪切模量、泊松比等力学参数的测量,适用于各类材料非均匀变形场的测量。
2、压缩应变测量
通过抗压试验可测定材料的抗压强度,XTDIC系统对于脆性材料其极限强度可快速测定,对于多异向性材料可测定变形极限作为强度标准。此次测试的样件为碳纤维复合材料,除测定抗压强度外,还可测定压力——应变曲线和弹性模量等,并输出全场应变试验数据。
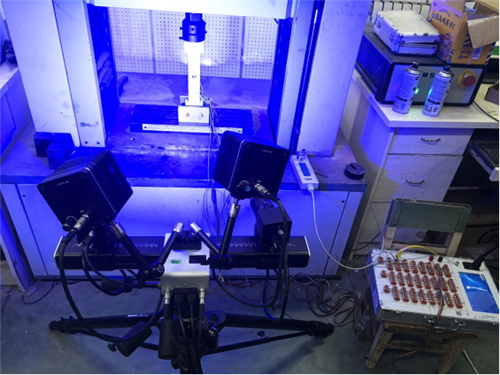
XTDIC系统可快速计算试件压缩加载全场位移,测试出试件受压变形位置,变形极限,表面破坏等演化过程,位移场如下所示:
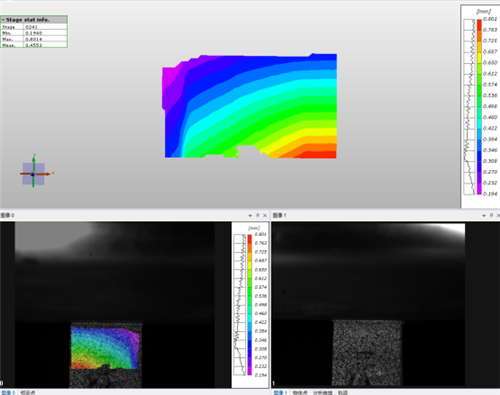
基于位移进行数值微分处理得到应变场,碳纤维复合材料在压缩加载过程的应变场,如下图所示:
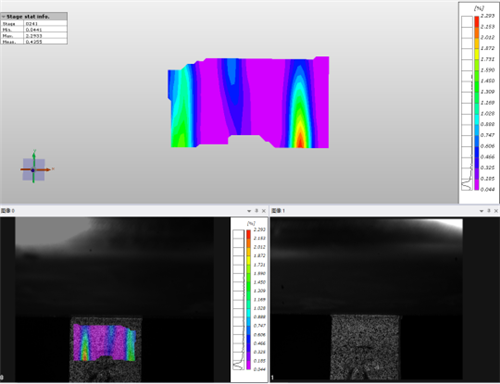
碳纤维复合材料在劈裂过程中,截取局部关键点反映其力学性能,输出应变数据:
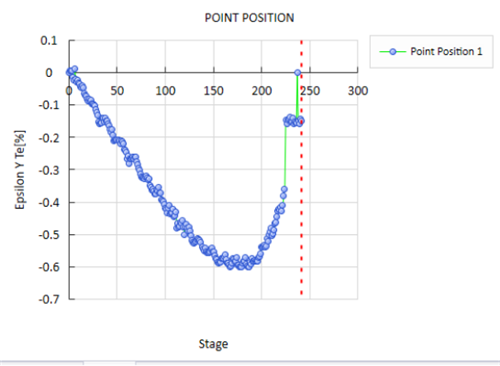
压缩实验是材料力学性能实验中基本的实验,它对评定材料的基本力学性能关系最密切。对于材料的使用需考量其压缩强度,这有助于分析材料的负载性能,改进材料本身抗压的结构性能,抗压试验的作用和意义就显得尤为重要。
使用XTDIC系统记录材料样品的拉伸、劈裂、压缩试验的实验数据,系统搭配的工业相机可记录材料样品在各种情况下(从静态荷载到动态荷载条件/失效)的变形情况,从全场测量区域进行测量,数据稳定,测量结果可视化,以便做进一步的分析评估,成为材料力学试验的理想分析工具。