手机新品及量产机型的材料和部件,在研发和生产过程中,需制定严苛的检验、检查及判定标准,确保研制的手机在量产前后各项性能指标满足品质及客户要求。
手机部件力学测试,涵盖了产品外观、结构可靠性与寿命测试,主要有折弯测试,材料韧性测试,高低温冲击应力测试,跌落测试等,由于部件材料选项众多,客户对手机部件的安全性能要求增高,如何测试产品的性能提高研发效率,成为业内关注的焦点。
三维全场应变测量技术的优势
采用三维全场应变测量技术(DIC技术),对材料进行力学测试,可有效降低研发成本和周期,高效对成品进行性能测试,数据分析与可视化呈现,保证产品质量。
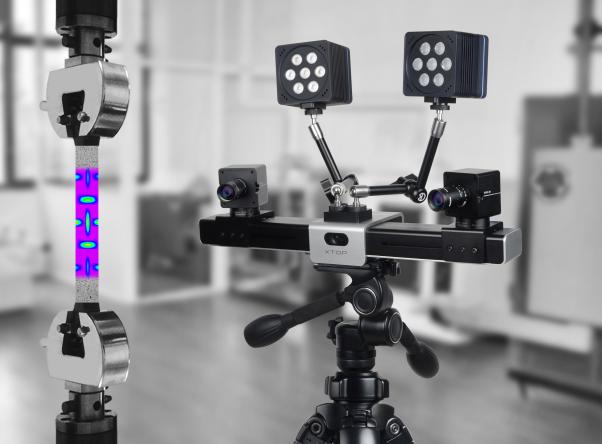
微小手机元器件性能检测
体视显微镜与双目相机的结合,基于DIC变形检测分析算法,三维显微应变测量技术实现微米级别的变形检测量,为PCB板,焊点等元器件提供变形检测方案。
通用结构力学性能测试
DIC变形检测分析算法,三维全场应变测量技术搭配高速工业相机,实现多种测量范围的变形检测,完美匹配屏幕折弯,手机跌落等性能检测需求。
新拓三维自主研发的XTDIC三维全场应变测量系统,结合数字图像相关技术(DIC)与双目立体视觉技术,通过追踪物体表面的散斑图像,实现变形过程中物体表面的三维坐标、位移场及应变场的测量,具有便携、速度快、精度高、易操作等特点;
与双目立体式显微镜技术结合,实现微小物体变形过程中表面的三维坐标、位移场及应变场的测量。
XTDIC三维全场应变测量系统在手机结构力学测试领域有众多应用优势,一是实时测量,可以实时进行三维全场应变计算,具备在线和离线两种计算处理模式,支持计算结果的UDP等方式实时输出。
二是XTDIC三维全场应变测量系统配置灵活,使用几千帧频到百万帧频的高速工业相机,捕捉高速运动的物体的图片,从而测量出高速状态下的三维全场变形。
三是XTDIC三维全场应变测量系统应用范围广,从二维检测到三维检测,从手机零件,元器件,整机的性能测试,到FEM验证,均可应用。
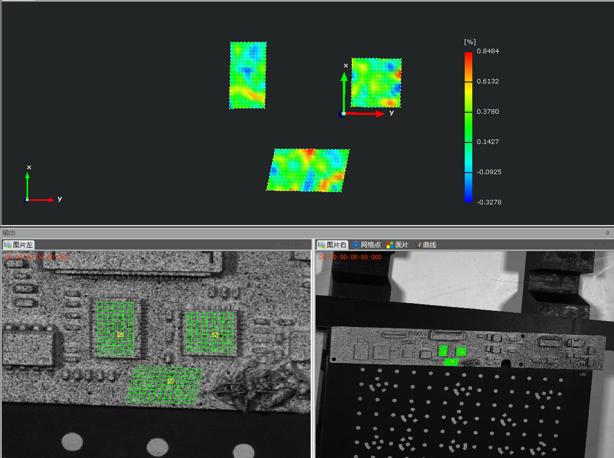
完整的XTDIC三维全场应变测量系统检测流程分为四步:准备现场、图像采集、计算分析。
1、现场准备是按照测量需求,对工件表面进行图案制备,固定采集设备等准备工作。
2、图像采集是按照测试规范,使用高速相机完整记录整个工件的变形过程。
3、计算分析是对采集到的的图像进行分析,得到完整的3D变形结果,并在此基础上,进行点、线等特征分析,并绘制曲线,输出报告
三维全场应变测量技术用于芯片与PCB板应力检测
低温几乎对所有的基本材料都有不利的影响,由于低温会改变其组成材料的物理特性,因此可能会改变其工作性能,对手机功能造成暂时或永久的损害。因此需要测试该芯片(<5mm)与PCB板在低温下的性能。
应变片只能测量单点单向的应变,不能进行全场检测。应变片只能是凭借仿真和模拟结果,预估应变位置然后进行粘贴,存在较大误差。
三维全场应变测量技术检测的效果:
完整检测出在高低温变化情况下,芯片表面发生的应变;可以检测出芯片表面任一点的变形数据,并绘制曲线;一次实验可以分析多种数据结果,相当于用一组实验替代原有的多组实验,节约成本和时间。
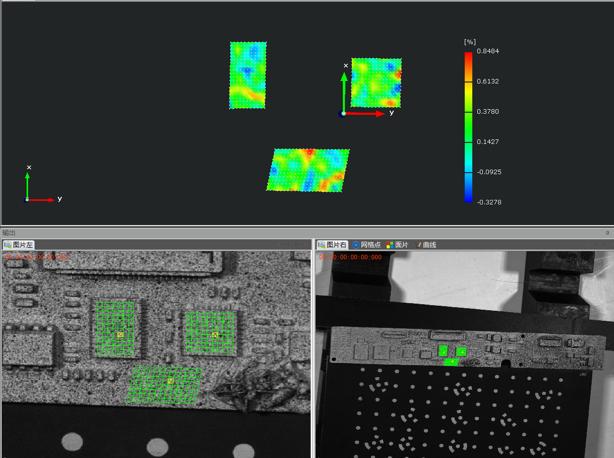
三维全场应变测量技术用于手机屏幕折弯检测
检测手机玻璃在折弯过程中的应变变化,分析该手机玻璃的力学性能是否符合FEM模拟结果和安全标准。屏幕尺寸:<200mm×100mm
应变片通常只能测量平面应变,不能测量三维的应变,尤其是折弯处的应变数据。在玻璃上粘贴标志点,可能会对玻璃的表面力学性能带来影响,影响最终的数据结果。
三维全场应变测量技术检测的效果:
完整的检测出手机屏幕在折弯过程中,表面应变的变化,验证FEM模拟的结果。不仅能够分析表面应变,3D数据还能分析折弯角度等数据,实现一机多用,节约设备成本和时间成本。
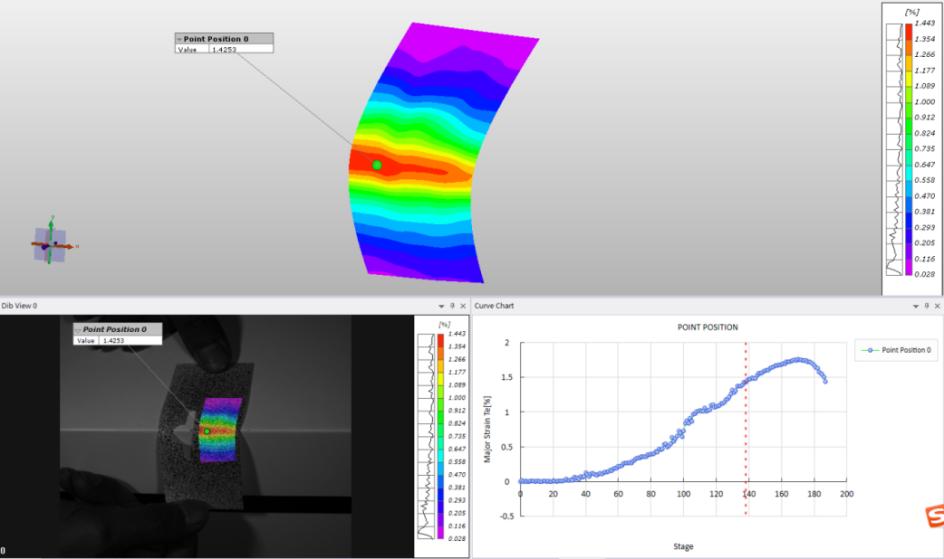
三维全场应变测量技术用于手机部件焊点检测
焊点在产品装配、搬运等过程中,线缆存在弯曲、扭转、摆动、拉伸等情况,导致焊点受力; 焊点尺寸:1.5mm*φ1mm(柱体)。
应变片的尺寸已经覆盖完整的焊点表面,所测结果存在较大误差,已经不能应用到实际的工作中。应变片由人工粘贴, 人工因素对数据的准确性影响很大。
三维全场应变测量技术检测的效果:
使用显微DIC全场应变测量技术,可以得到小尺寸焊点的表面应变数据。3D检测手段,还能够完整重建圆柱表面的三维数据,计算焊点的尺寸信息。
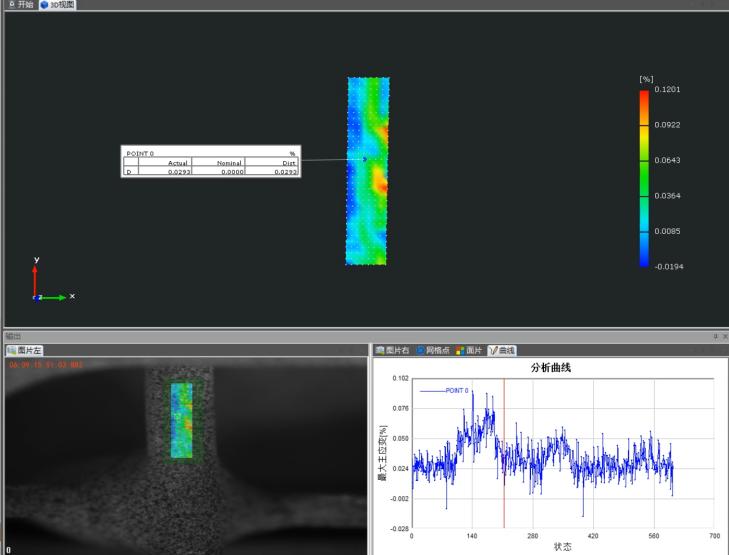