金属材料看起来无所不能,它被广泛来制作机器、兵刃、舰船、飞机等等。其实,金属也有它的短处,在长期服役状态下,可以产生疲劳状态。统计数据表明,机械零件的失效,约有70%左右是疲劳引起的,而且造成的事故大多数是灾难性的。
航空客机叶片断裂金属疲劳
飞机金属零部件疲劳折断
1979年525日,一架载乖客的美国航空公司DG-10型巨型客机,从芝加哥起飞不久,就失去了左边一具引擎,随即着火燃烧,随即坠毁在地。。机上273名乘客和机组人员无一免。这是世界航空史上最悲惨的事件之一。
事后,有关当局对这架失事飞机的残骸进行检查后发现,这架飞机上连接一具引擎与机翼的螺栓因金属疲劳折断,从而导致引擎燃烧爆炸。
高速列车部件疲劳断裂
1998年6月3日,由慕尼黑开往汉保的德国ICE884次高速列车在运行至距汉诺威东北方向附近的小镇埃舍德时,发生了第二次世界大战后德国最为惨重的列车脱轨行车事故。事故发生后12辆拖车全部脱轨。造成101人死亡,88人重伤。
事后经分析,该列车的橡胶弹性车轮是引起本次事故的原因之一。该列车的轮箍是轧制的无缝钢圈,通过热效应压在轮心上,轮心是铸钢轮体,中间有一层橡胶体。轮箍轧制时残留气泡或矿碴,在高压负荷动力作用下,就可能开裂,当然也可能是由于轮箍材料老化产生“疲劳断裂”所致。
由于金属材料的疲劳一般难以发现,因此常造成突然的事故。在第二次世界大战期间,美国的5千艘货船共发生1千多次破坏事故,有238艘完全报废,其中大部分要归咎于金属材料的疲劳。
关于金属疲劳
疲劳是材料(金属)承受循环应力或应变作用时,结构性能下降,并最终导致破坏的现象。疲劳失效是最常见的失效形式之一。根据相关文献提供的数据显示,各种机械中,疲劳失效的零件占失效零件的60~70%。疲劳断裂失效原则上属于低应力脆断失效,疲劳中难以观察到明显的塑性变形,因为这是以局部塑性变形为主,且主要发生在结构的固有缺陷上。虽然频率对疲劳失效有一定影响,但多数情况下疲劳失效主要与循环次数有关。
按引起疲劳失效的应力特点可以分为:由机械应力引起的机械疲劳和热应力(交变热应力)引起的热疲劳;
从循环周次可分为:高周、低周、超高周疲劳;根据载荷性质可分为:拉-压疲劳、扭转疲劳以及弯曲疲劳等;
根据工件的工作环境可分为:腐蚀疲劳、低温疲劳、高温疲劳。
传统应变测量手段
对于疲劳加载试验,传统的应变测量手段有:应变片、引伸计等等;传统应变测量手段精度高,但是也存在很多不足:
接触式测量,有些部位不好夹持,如孔的变形测量等等;
信息量有限,只能测量到少量局部的点,未能及时发现局部塑性变形区域;
引伸计测量的是工程应变;
新拓三维全场应变实时测量技术方案
新拓三维经过十余年的技术研发创新,为疲劳加载试验提供先进的解决方案。XTDIC三维光学全场应变测量系统可以实现全场应变实时测量,对零部件在功能和行为方面进行动态变形测量, 评估扭曲、弯曲、位移、速度和加速度等因素,分析零件在使用过程中的安全风险、零件寿命、蠕变、老化及外观变化。主要有以下特点:
全场实时3D位移、应变测量;
全场离线3D位移、应变测量,应力场重构;
强度、振动分析,耐久度分析;
有限元验证与评估;
颈缩实时测量并反馈;
对于稳态疲劳加载试验,XTDIC三维光学全场应变测量系统采用相位同步精准触发方式采集数据。通过软件系统读取疲劳试验机的加载信号,通过设置触发相位来控制相机进行精准的数据采集。
其具有以下特点:
可以实现对某个特殊相位如波峰、波谷、特定相位时刻的图像进行采集;通过先进的相位同步采集技术,XTDIC系统可以实现疲劳全场3D位移和应变测量,应力场重构。
疲劳加载断裂测试
XTDIC三维光学全场应变测量系统的疲劳测量技术的另一大亮点之处在于实时测量。系统可以实现疲劳全场3D位移和应变的实时测量的同时,还可以实时与试验机数据关联,绘制应力应变曲线图等后处理使用。
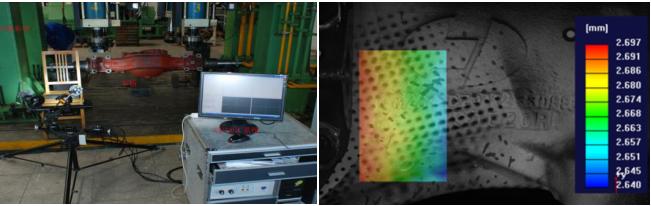
新拓DIC-机构件加载疲劳测试
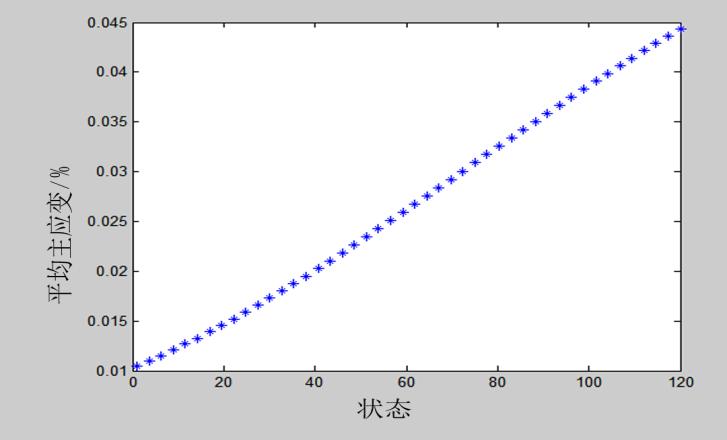
被测区域平均主应变曲线
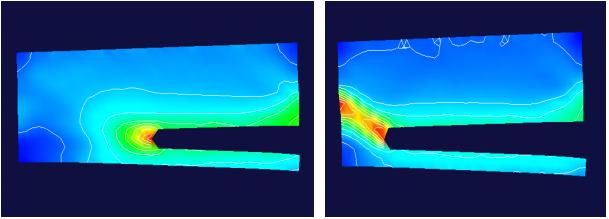
断裂过程中的应变分布
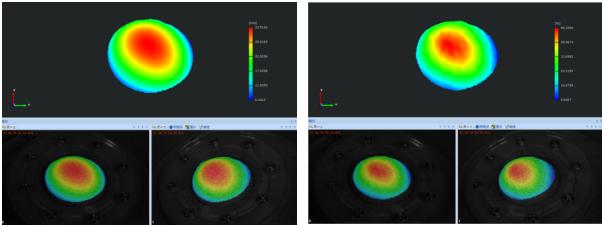
材料胀形应力-应变数据