蓝光工业级三维扫描仪,是工业制造三维数字化应用的重要工具,它能够快速获取高精度三维结构模型,也是3D打印产业上游,无论是工业还是消费级3D打印,其设计和生产都可以用高精度三维扫描仪来助力逆向设计。自动化三维扫描建模给3D打印带来了极大的便利,新拓三维自主研发的蓝光3D扫描仪能够快速采集逼真3D模型数据,支持导入到主流3D设计软件中,并支持3D打印输出。
在工业制造领域,三维扫描仪和3D打印的结合应用已成为一种趋势,并将广泛的应用在设计领域,尤其是工业设计,产品开模类复杂的产品中。3D打印可以在数小时内完成一个模具的打印,节约产品从研发到投入市场的大量时间。
蓝光三维扫描仪可用于工业产品造型,产品工业设计,三维数模获取,模具设计,零部件形状扫描与尺寸检测等。3D 打印机通过各种原料打印3D模型,使用3D 辅助设计软件,设计出复杂精密的零部件及产品,然后用3D打印机进行打印。快速成形技术其常在模具制造、工业设计等领域,现在正逐渐用于一些产品的直接制造。
模具领域
利用3D打印工艺能够在模具内部做出3D随形水路,提升模具的冷却效率,缩短注塑周期,目前,金属3D打印技术已经被深入运用于注塑模具量产中。比如包括汽车、办公设备、家电等企业,采用快速成形技术来提高产品的成形效率和品质的方法已成为常态。
3D打印模具在模具行业应用越来越广泛,如何设计好模具浇口套的3D异形水路,这将直接关系到模具批量制造的效率及冷却效果。针对3D打印模具设计及分析,提供以下对比:
传统工艺流程:设计图纸-订料-钻水路-CNC粗加工-热处理-CNC精加工(加工工艺繁琐,冷却水路分布不均匀,受结构限制)
金属3D打印工艺流程:设计图纸-金属3D打印-CNC精加工(加工效率高,速度快,不受结构限制)
以往模具的加工余量检测,主要是使用三坐标划线机,编程人员事先以提供加工型面的理论数值;检测人员只能根据对应位置去检测,对照数据去判定余量大小;模具尺寸偏差,难于判断工艺存在问题,无法从整体型面去做偏差分析。采用三维扫描仪,对毛坯模具表面进行点云数据的获取,可以全尺寸获取模具的三维模型,精度高,数据完整。

工业领域
3D打印技术在工业领域的应用,重点是解决传统制造技术无法解决的高难度、复杂的、个性化设计制造的难题。对于结构复杂的零件,3D打印技术可以实现整体打印成形,避免复杂零件进行分拆制造,然后焊接成形带来的质量增大和潜在的质量缺陷,甚至能够取消复杂零部件的装配。
蓝光三维扫描仪可对工业零部件进行三维扫描,获得立体三维数据后,与原始CAD数模进行拟合+3D对比,验证工件每个位置的偏差。可用于零部件、模具、检具等进行质量检测。将扫描数据和原始CAD模型同时导入检测软件,对其进行形位公差标注分析。对无图纸的零部件进行三维扫描,通过软件进行逆向工程,转为数字化CAD模型,对其进行正向二次设计开发。
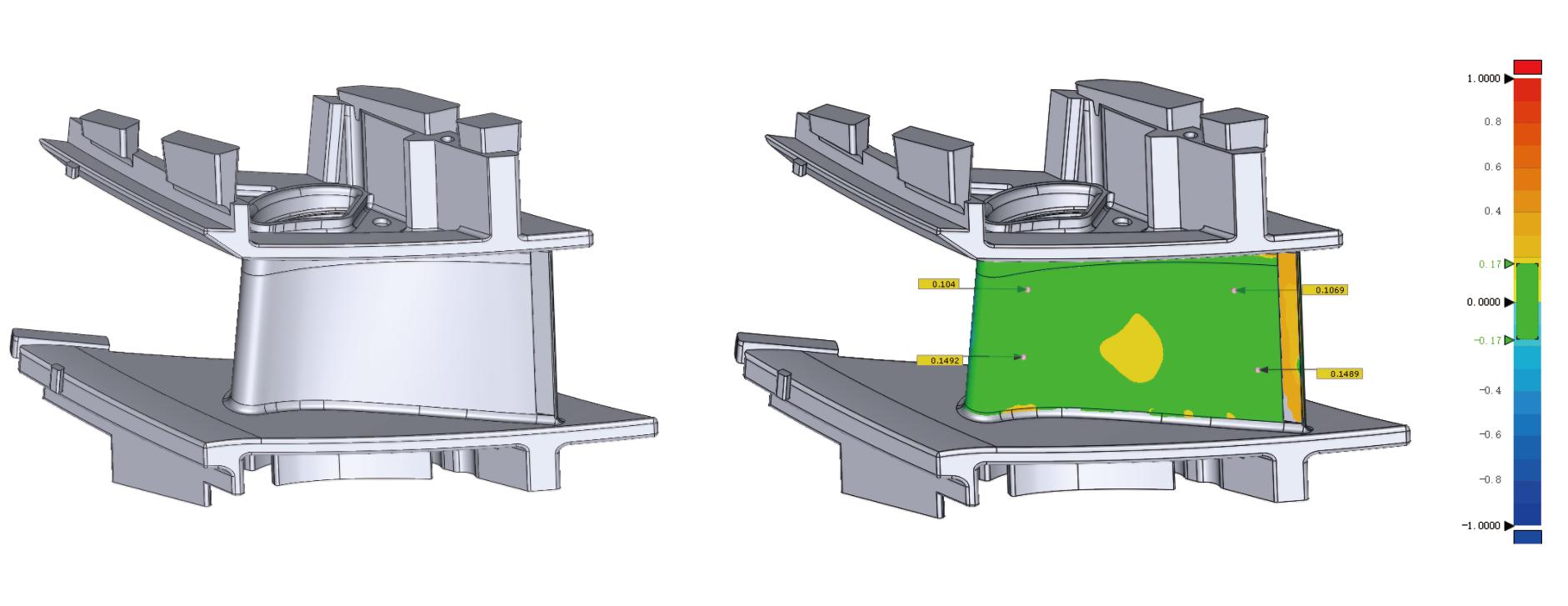
3D打印领域
无需复杂传统加工程序或模具,3D打印可将概念设计转化成实体,缩短外形验证及功能性验证周期,提高研发效率;与传统工业相比,3D打印可以整合多个零件,变成一个功能零件,节约原材料,显著降低制造、组装成本;可优化复杂零部件的结构,减轻零件重量,轻松实现大型装配组件轻量化。
高端制造需要众多精密的机械零部件和装备,其几何形态和尺寸是否达到设计标准,需要借助工业级三维扫描仪对其进行全尺寸测量,定位具体位置的尺寸偏差,才能更好地满足结构的装配和载荷性能,提制造效率。伴随着计算机、数字化技术在制造行业的应用发展,高端制造技术发生了根本性变革,三维光学测量技术已经渗透并成果应用于汽车制造、模具制造、3C电子、精密注塑、复杂轮廓零部件等各个环节。
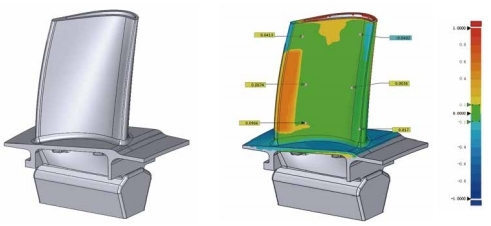
汽车领域
3D打印,可灵活制造,特别适合复杂组件、复杂零部件及薄壁件的制作;不需任何额外工具,无需铸造、压铸,缩短开发时间,大大降低开发成本。3D打印用于实验模型和功能原型的制作,可实现快速修改设计方案并反复大量迭代。在确保原型产品设计质量的同时,大大缩短产品设计和原型开发所需的时间,提高研发效率。
对汽车行业来说,蓝光工业级三维扫描仪不管是从设计-研发-小批量试制-大批量制造,在逆向设计和质量检测上来说,相对传统的接触式测量方法都有着明显的优势。3D扫描仪目前应用主要有复杂结构零部件的全尺寸检测,汽车上的轻量化结构零件尺寸控制,整车模型的三维逆向设计,用于逆向设计;三维扫描技术使得部件生产更高质量,因此大大缩短了开发时间和生产成本。可重复生产出尺寸更精密、更轻更好的零部件,直接安装在车辆上。
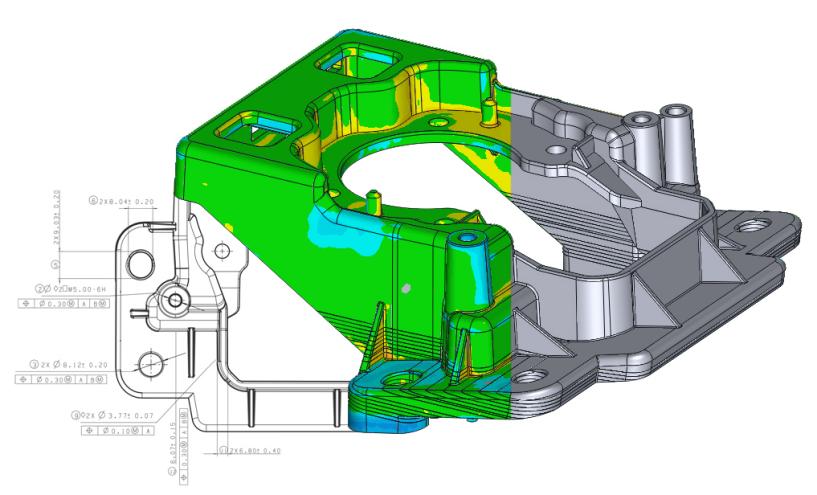